Critical work shopping kit index
Critical Work shopping: The Contact Microphone
Ellen K. Foster
Rensselaer Polytechnic Institute
Building a Contact Microphone // Starting out on Soldering
A contact microphone is a quick and easy Do It Yourself (DIY) musical component that can make basically any object into an instrument. Instead of amplifying reverberating sound waves, the piezo element of a contact microphone picks up the material vibrations of an object. It will amplify the rustling of paper (if it is in touch with the paper), a tap dancer's jumps and kicks on a piece of metal (if it is connected to said metal) and the vibrations coming from your throat (put your hand to your throat and hum with mouth closed. Feel those vibrations? A contact mic would pick that up.)
The materials to build a contact microphone are fairly easy to get, either through bulk online or at a local electronics store or RadioShack.
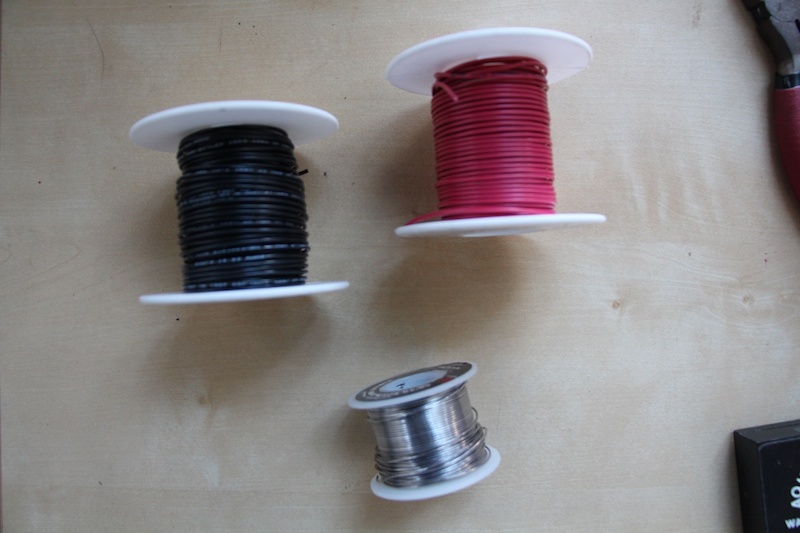
The two spools at the top of this image are red and black single 22 gauge single-stranded wire, which will be used to make the cable of the contact microphone, connecting the 1/8 inch jack to the piezo element. Below is a picture of the 1/8 inch stereo plug that the wires will be attached to. You can also use a 1/4 inch plug, or a jack. Some contact microphone builders include particular circuitry to get the contact microphone to make particular sounds. We will be building the simplest variation on these themes.
The 1/8 inch plug will come the way it is on the left, and so you will want to unscrew the casing to get to the inside of the plug for soldering.
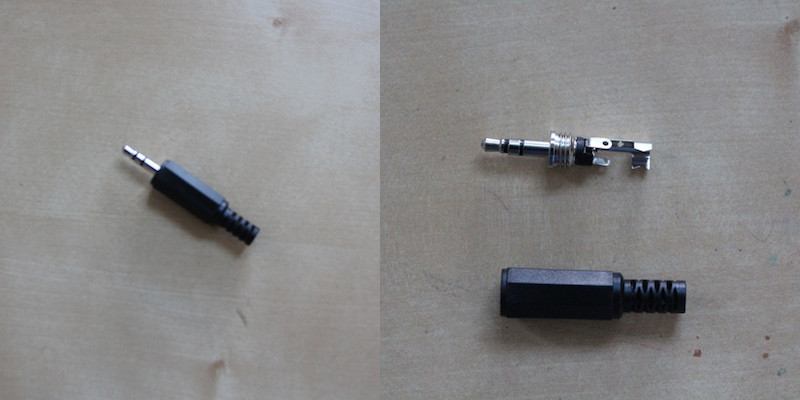
Note that there is a longer prong (which is connected to the grounding element of the plug) and then two smaller prongs opposite one another (this connects to the signal element of the plug). You will want to make sure the wire soldered through the signal holes attaches to the signal part of the piezo disk, and that the wire soldered through the grounding hole attaches to the outer, grounded part of the piezo disk.
The piezo element, which picks up on vibrations, can be acquired through various means.
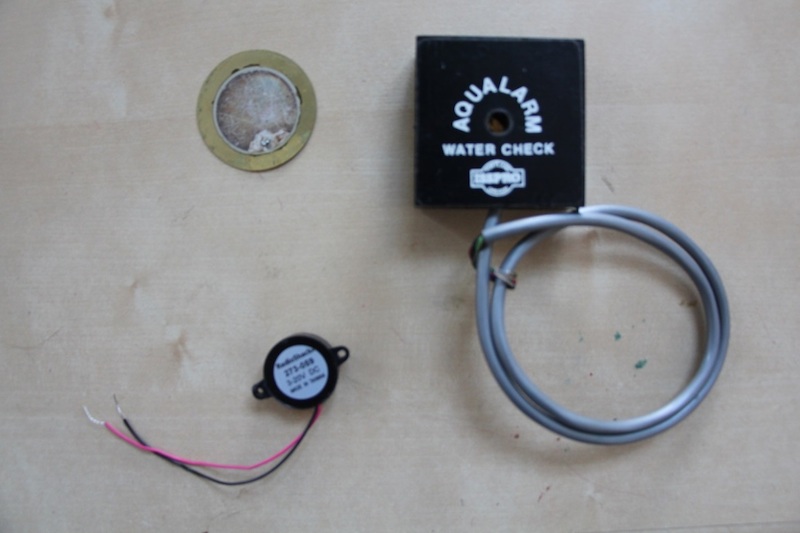
Pictured above are 3 different forms that the piezo disk may come in. The upper left piezo element is free of any encasing and is just the piezo element itself. If you order bulk piezo disks online, they will most likely come like this, possibly with two wires, typically a black one coming from the ground (the outer copper ring) and a red one coming from the signal producing part (the inner, grey-ish part).
The piezo buzzer element on the lower left was bought from a local RadioShack, and the water check monitor was given to me by a friend who acquired a number of them as a pile of electronic waste (e-waste). All would work just as well for building a contact microphone.
The tools used for this project are a soldering iron, pliers (if you decide to take the piezo element out of something, such as the buzzer from RadioShack), and wire cutters/strippers.
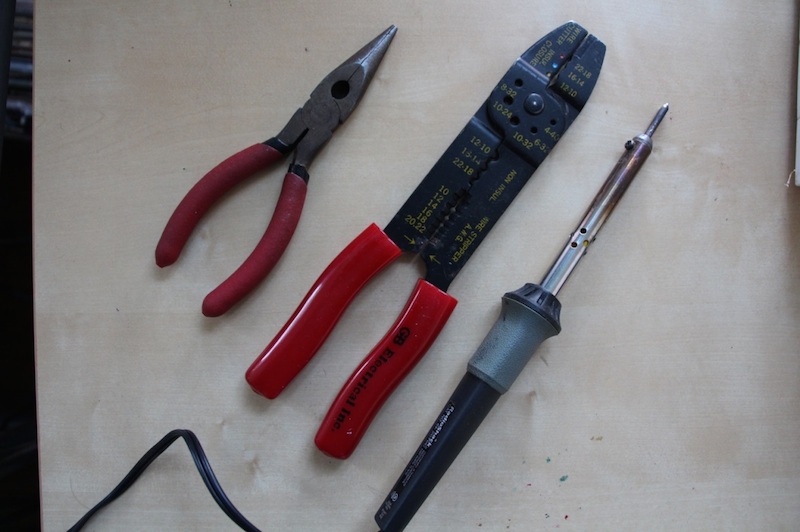
First cut two equal lengths of red and black wire for connecting the plug to the contact microphone.
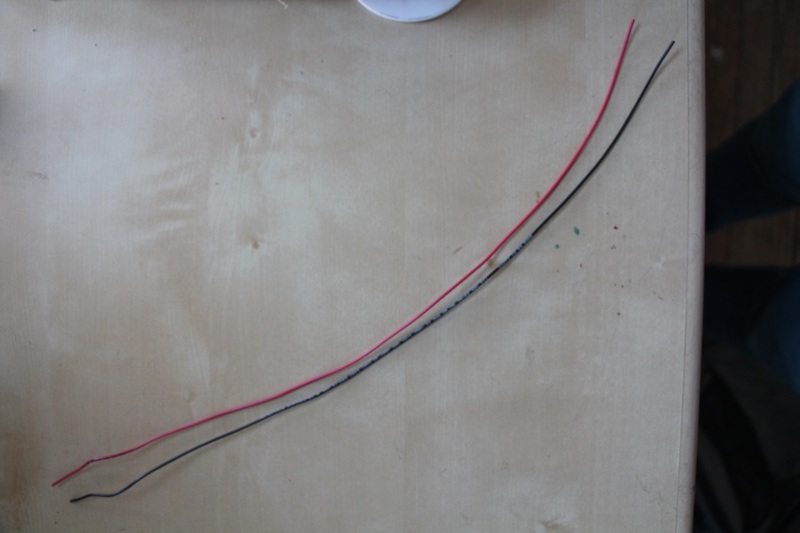
Next, strip both ends of the wires. Striping wire can be an art form in and of itself and will require that you have good strippers. The ones pictured (that I have) are good for many differently gauged wire. I used the smallest opening to strip my wire, stripping about 1/2 inch off of either end. Your wires should look like this on either end, with that 1/2 inch stripped.
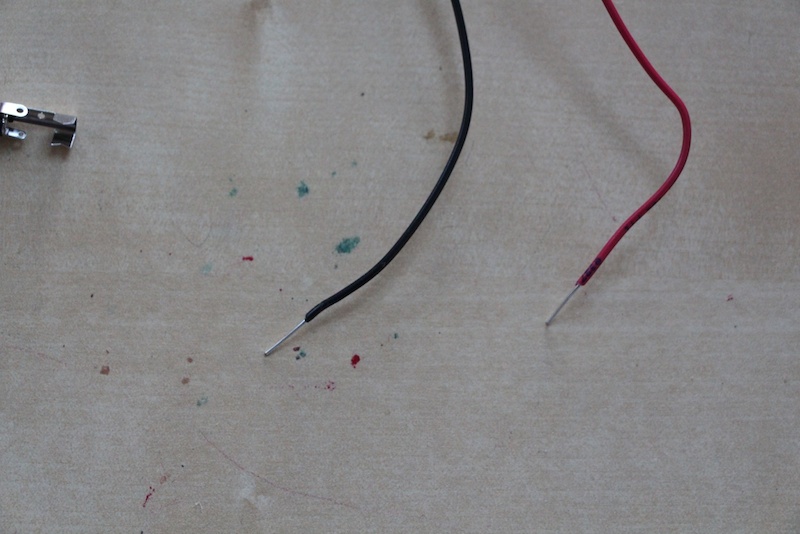
First, I like to solder the wires to the plug and get that part stable before soldering them to the piezo element.
Before soldering the wire, I bend the stripped part of the red wire through the hole on the back of the grounded part of the exposed inner-workings of the plug. I typically thread it through so the rest of the wire is on the inside. This way it is easier to screw the casing back on.
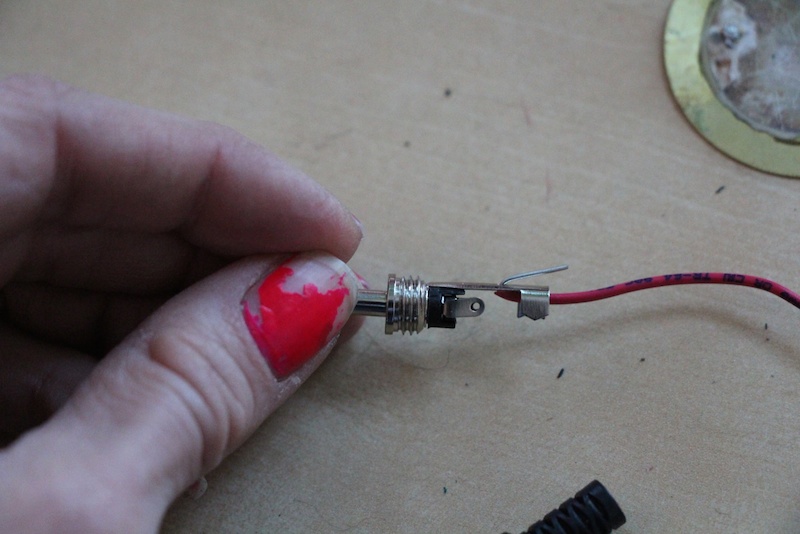
Solder the outside point and then get ready to thread the other wire through the two holes of the tips on the more inner part of the plug. Again, this is the positive part of the plug. The two holes are easier to see in the following picture:
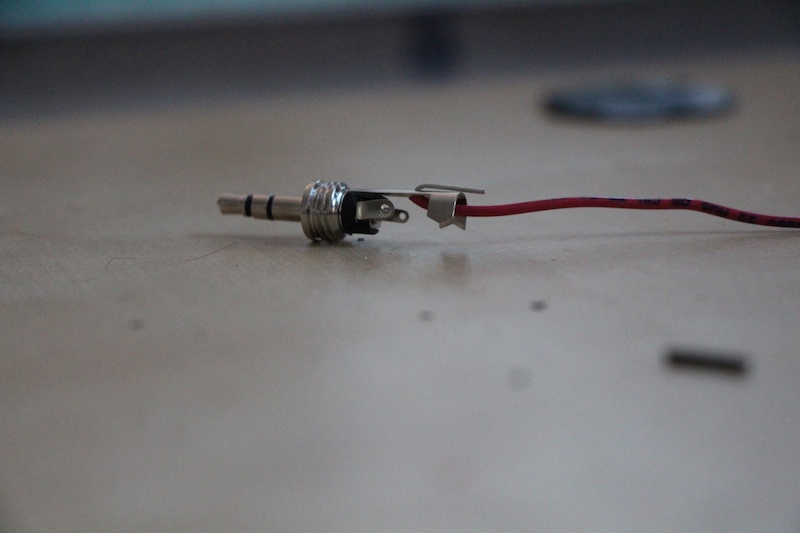
Plug in and turn on (if need be as some soldering irons automatically turn on when you plug them in) your soldering iron. Wait a few minutes for the iron to heat up before using it, but do not touch the iron to test its heat. The soldering iron is extremely hot to the touch and will burn you. You will want to tin the tip with a bit solder before starting. This involves coating the soldering iron with a bit of solder.

Notice the fumes. You should have decent ventilation for any soldering project, however simple or complex — although I have sometimes gotten away without. When soldering, you want to touch the soldering iron to the joint where the two pieces of wire meet, and not directly touch the solder to the iron. Often the solder will flow onto or stick to the iron tip if you do this. Tinning the tip also helps to reduce solder from sticking to the soldering iron.
A way to help the solder flow into the joint (instead of sticking to the iron) is to use flux, something which I do not use, but which my colleague Lindsay Karty swears by. If you have flux and want to use it, you can dip the end of the exposed wire into the flux before putting it through the hole in the plug. Flux is typically gooey pinkish/orange stuff that comes in a round container, like shoe polish.
Below is the result of soldering the grounding contact of the plug and the red wire together.
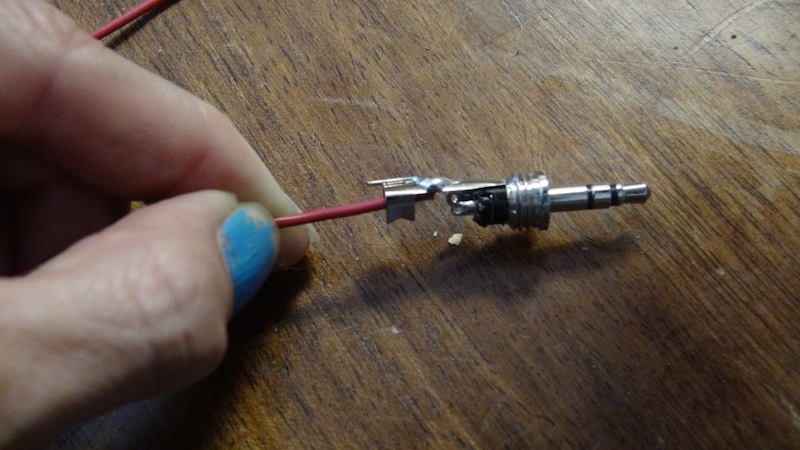
I used wire cutters to clip off some of the extra wire beyond the solder point.
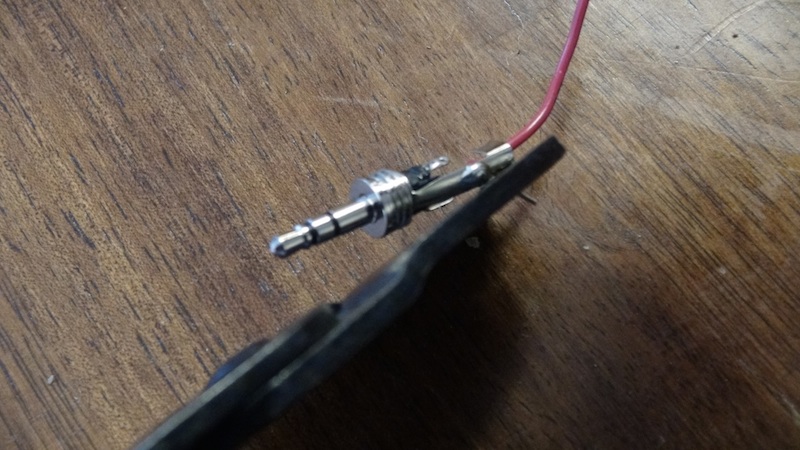
Next, take the other wire and thread it through both of the holes easily displayed above, making sure there is not much excess beyond the final hole. You can use wire clippers to cut any excess wire sticking out. Make sure the two wires are close together so that they will be easy to secure and slip into the outside casing.
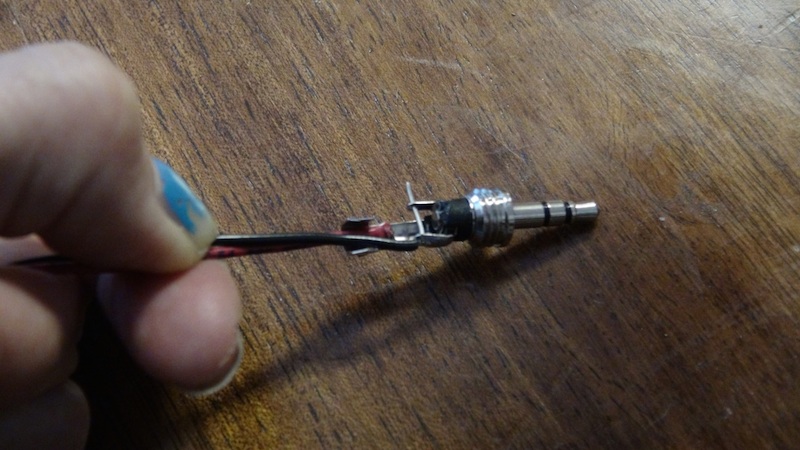
Make your second soldered point by soldering the end of the wire to the first hole. To be extra secure, you can solder the second hole as well.
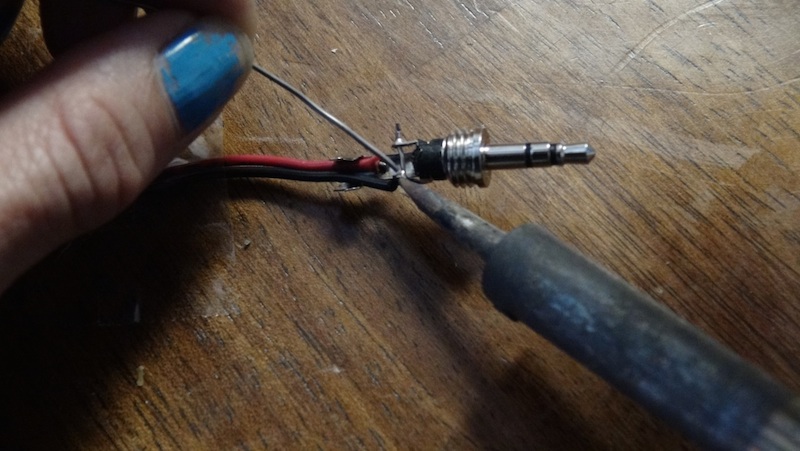
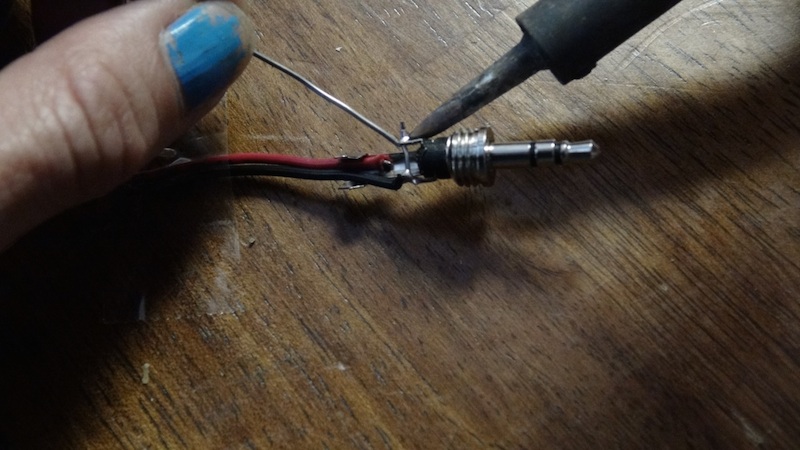
After soldering, I cut the extra wire sticking out so the cover might fit better, which you can see below.
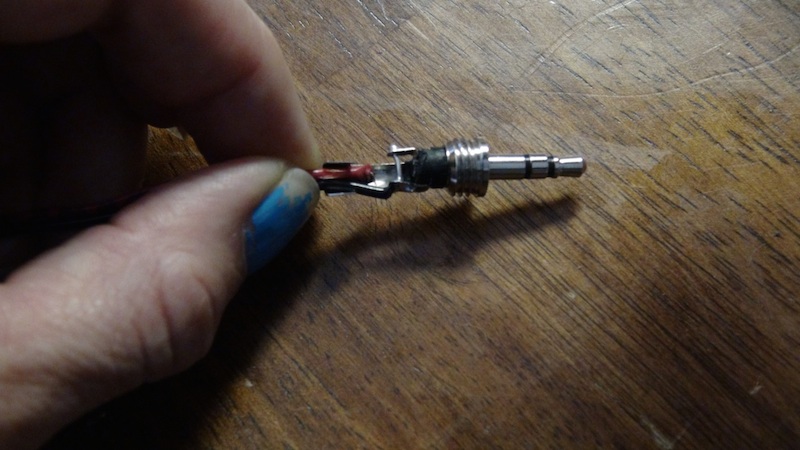
Now that the two wires are soldered in place, you can crimp them down.
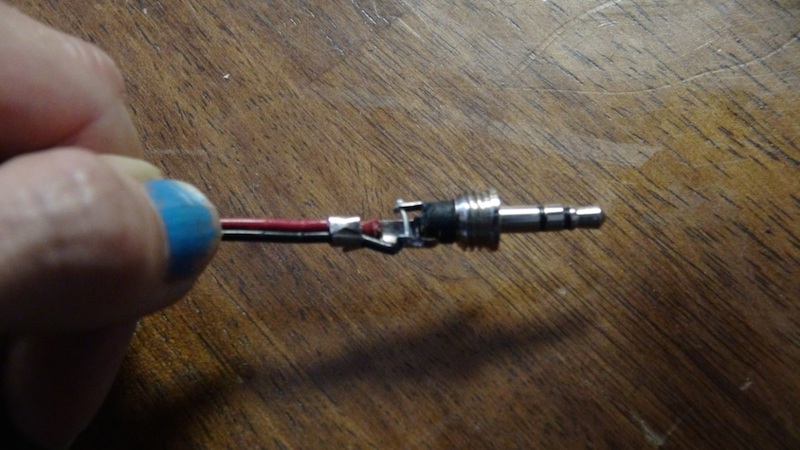
And slip the casing back on, threading the wires through and screwing it securely on. If you are having difficulty slipping the casing back on, you may want to re-do some of the soldering, or make sure the wires are close together. It can be tricky and might be a tight fit.
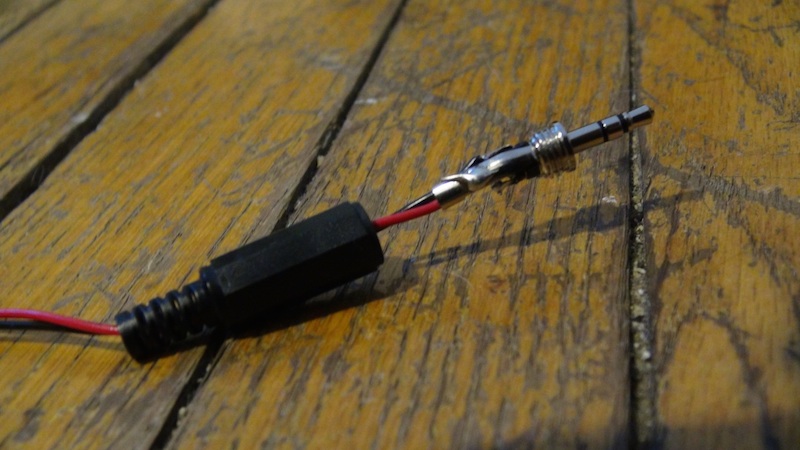
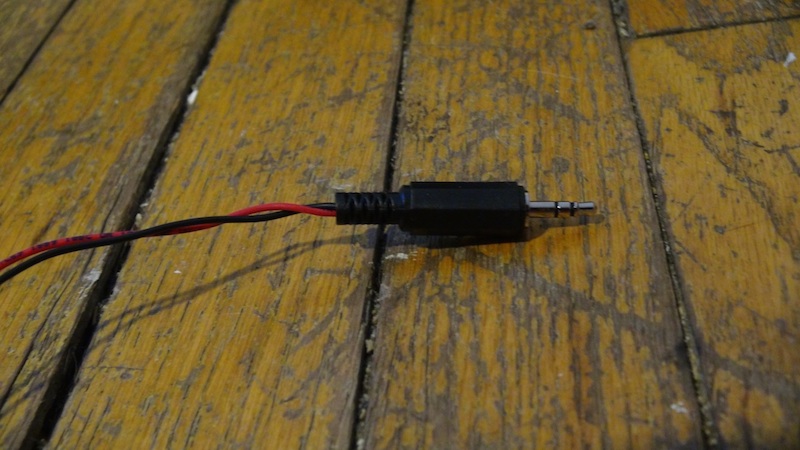
The next two soldered contacts will be on the piezo element itself. The outer ring of the piezo element is known as the ground, so the wire coming from the sleeve of the plug should go connect to the outer ring of the piezo disk (in this case, the red wire). Then, the inner part of the piezo disk carries the signal. The wire coming from the tip of the plug should connect to this part of the disk (in this case, the black wire).
I have found that prepping the piezo disk by melting solder onto it beforehand works quite well. I did this for both wire placements.
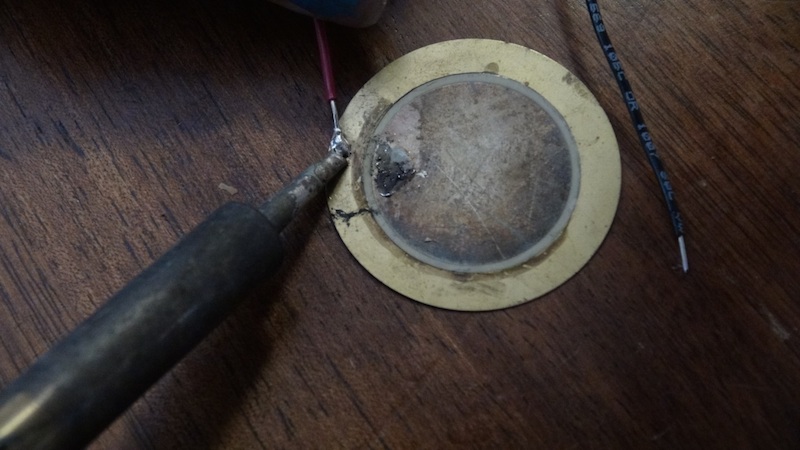
While heating up the solder already placed on the disk, you can place the wire in the now fluid solder, take away the hot iron, and the joint will be created. Above the joint is in the process of being made, below it is complete.
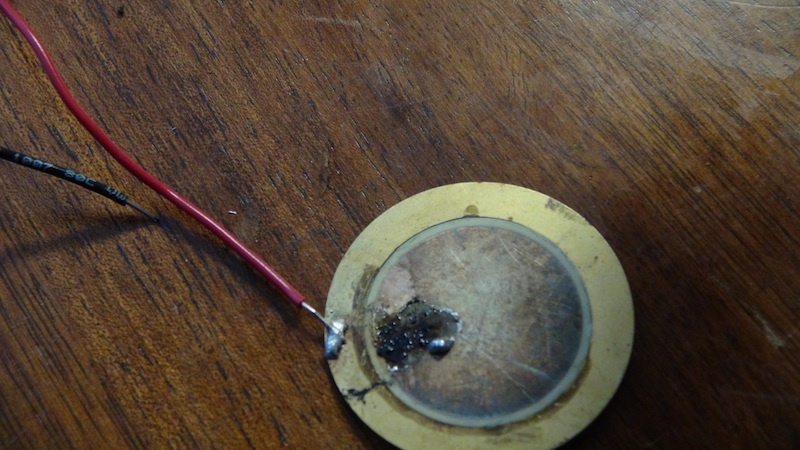
Notice I have already placed some solder in the middle of the disk for the black wire, which in this case is the signal wire. Sometimes it can be tricky to get the solder to stick well in this middle part of the piezo, so it might take a few tries and some patience. In order to make the soldering easier, I taped down the black wire and made sure it was flush with the piezo element where I wanted to solder and place them. Securing with tape will also be helpful if you do not melt solder on the disk prior to soldering the wire, as one hand will be then hold the solder while the other hand holds the soldering iron.
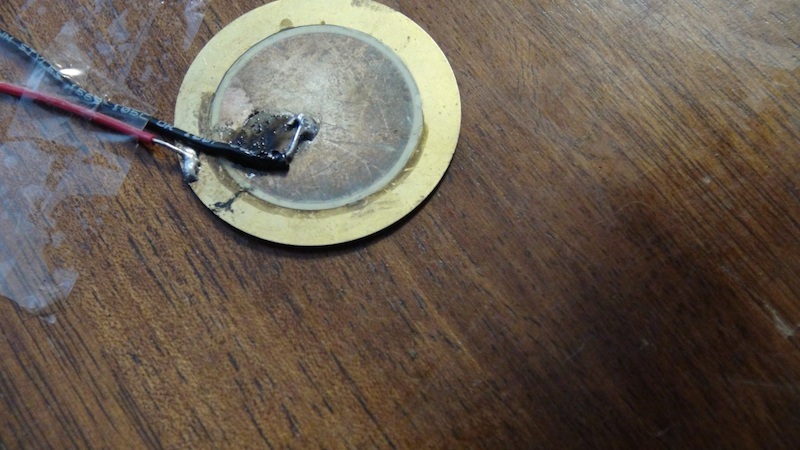
Once the two points of contact are secure, you can un-tape or pick up your contact microphone to make sure it is fully connected.
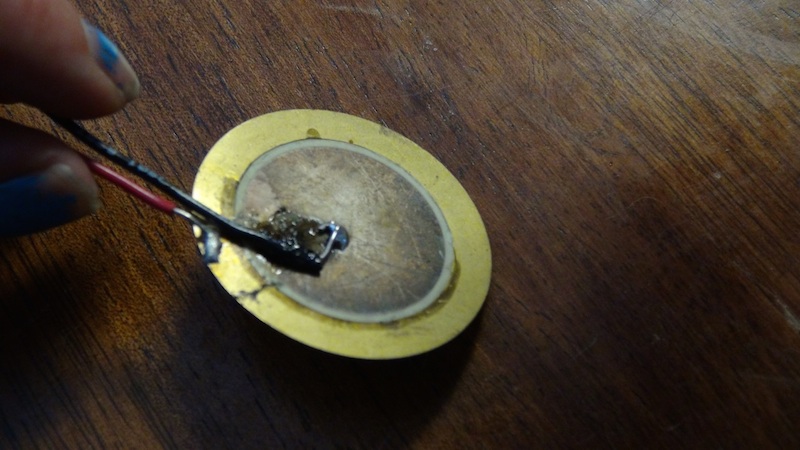
Handle the contact microphone with care, and if you want to deeply secure the joints, you can cover them in hot glue with a hot glue gun or some electric tape. Neither addition will greatly affect the efficacy of the contact microphone. Some contact microphone fabricators even use plasti-dip, a liquid plastic that you can dip objects into, and then let dry for a thin plastic coating that secures objects in place and protects the solder contacts. Any hardware store should have Plasti-Dip available, or you can order it on-line.
Now that you have finished you can test your contact mic. Small amps that take 1/8 inch plugs are easily available in electronics stores, and there are many variations on this instructional for other connections. This includes using a ¼ inch plug for larger amps, or a jack input for connecting a longer cable chord to the contact microphone. These are some design possibilities that you can change to meet your needs and in how you intend to use the contact microphone.
In terms of soldering technique, several instructional videos exist, as well as a comic book that walks you through the 'do's' and 'don'ts' of soldering. It can be found here. Getting handy with soldering often takes time, though, and everyone has their own little tricks, tips and ideas of how to solder in their own particular way. You can even make circuits using conductive ink, string and copper tape, taking out the need to solder for some simple projects, or even for very complex things that you want to be light-weight and wearable.